1.welding technology
1.Preparation before welding
1.1 Welders must hold a valid welder operation certificate for the corresponding qualified project before welding.
Before welding, the welding process technician must conduct a welding process briefing, and the welder must understand the requirements of the process manual before welding can be carried out.
1.3 Welding equipment and instruments must be intact and undamaged.
1.4 Strictly follow the welding specifications for operation, and welders are not allowed to make unauthorized changes.
Clean the welding joints and grooves to remove oil, dirt, and rust.
1.6 The welding rod used for spot welding should be the same as the formal welding rod, and the spot welding points should meet the requirements to prevent misalignment and deformation.
1.7 It is not allowed to randomly arc on the workpiece.
Requirements for welding environment conditions
2.1 Welding is strictly prohibited under any of the following circumstances:
2.1.1 Welding outdoors in rainy or snowy weather;
2.1.2 Wind speed: When welding rod arc welding is ≥ 10m/s and argon arc welding is ≥ 5m/s;
2.1.3 When the working environment temperature is ≤ 5 degrees Celsius and the humidity is ≥ 90%;
2.1.4 When there is combustible gas or flammable and explosive materials in the workplace.
Metal materials and welding materials
3.1 Before welding, the steel grade, mechanical properties, chemical composition, and factory certificate of conformity should be determined. Whether it meets the manufacturing requirements of the product or purchased parts.
3.2 Check that metal materials with defects such as cracks and double skin cannot be used.
3.3 Welding Materials:
3.3.1 Welding rods and wires must have factory certificates of conformity and be packaged intact.
3.3.2 Welding rods should be dried strictly according to the welding rod instructions or relevant regulations before use, and records should be kept. Oil stains, rust, etc. on the welding wire should be cleaned thoroughly before use.
3.3.3 Before use, each batch of welding rods must undergo a trial welding to evaluate their operational performance. The base material for the trial welding is the same as the welding rod material, and it can be used for single-sided multi-layer welding with a V-shaped groove. The operational performance of welding rods should meet the following requirements: easy arc initiation, stable arc combustion, and minimal splashing. The medicine skin melts evenly without deviating from the arc. Slag can evenly cover the weld metal and is easy to remove after cooling. The surface of the weld seam is smooth, aesthetically pleasing, and there are no pores, slag inclusions, or cracks inside the weld seam.
3.3.4 For welding of the same type of steel, the welding material should be selected based on the principle of equal strength to the base metal.
When welding two different grades of materials, the welding rod should be selected according to the material with the higher strength level.
Test welding of test specimens and inspection of weld seams of test specimens:
Before welding the product or component, it is necessary to conduct experimental welding and weld seam inspection on the base material used in the product to determine the feasibility of the welding process. Formal product welding can only be carried out after the welding inspection is qualified.
4.2 Experimental welding requires the production of welding test plates. The base material, welding material, and welding conditions used for welding test plates should be the same as the manufacturing conditions of the corresponding products or components.
4.3 If there are no clear provisions in the relevant standards or technical conditions, no less than 2 test blocks shall be cut from the welding test plate.
4.4 Select the electrode diameter, welding current, and number of welding layers for different material thicknesses according to the table below. After the experimental board is prepared, appropriate welding rods, electrode diameters, welding currents, and welding layers are selected for experimental welding based on the strength of the welded components, impact load requirements, component complexity, and the weldability and thickness of the base material.
4.5 Welding defects such as slag inclusion, porosity, undercutting, welding slip, incomplete penetration, cracks, and excessive height and width are not allowed in the welded parts.
5. Welding diagram:
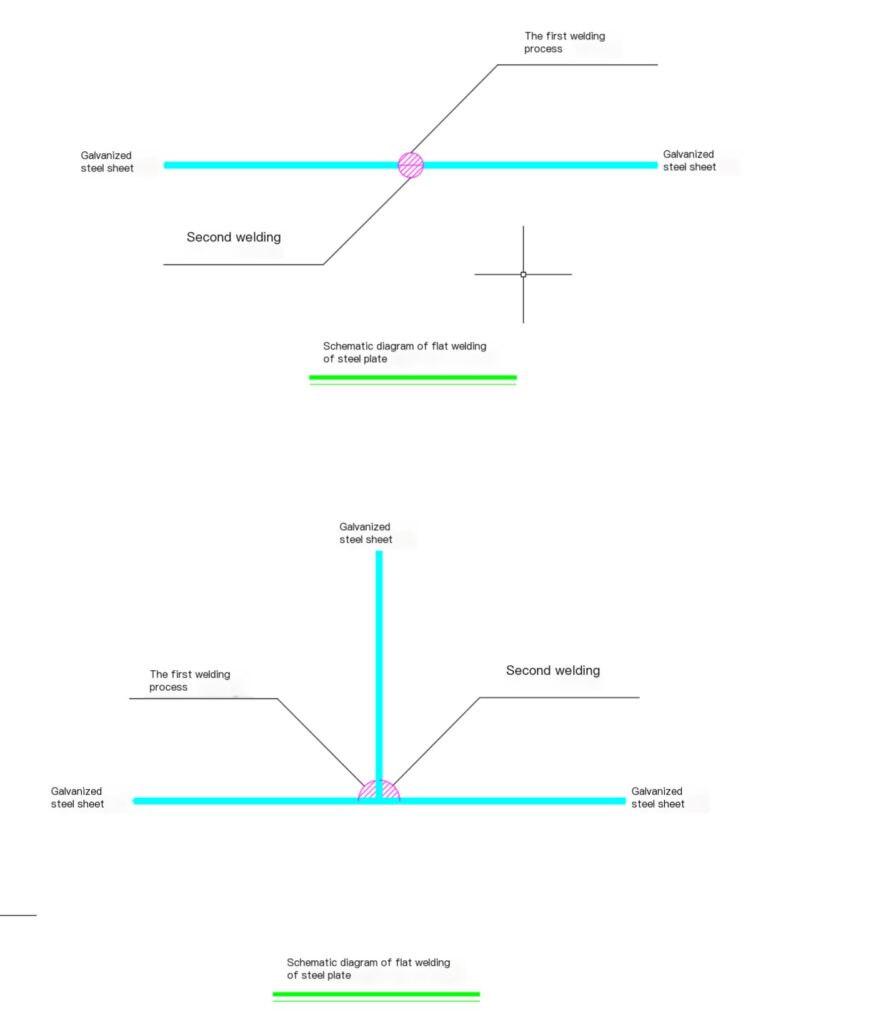
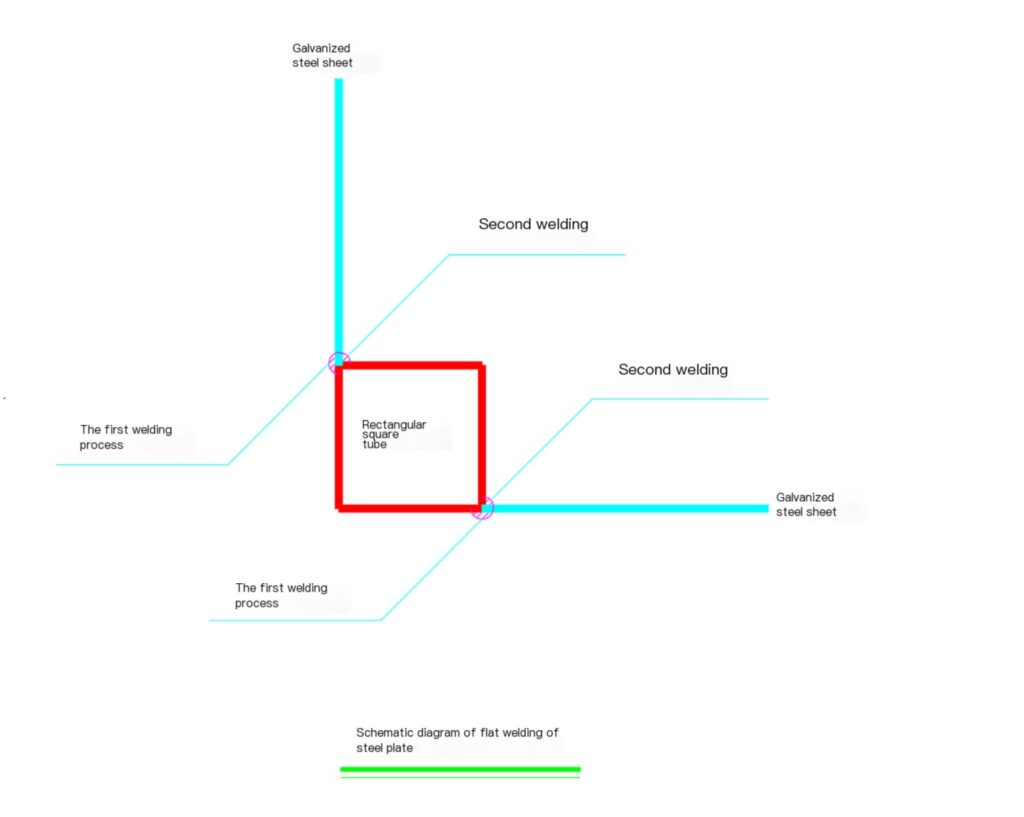
2.Anti corrosion process
1.The anti-corrosion service life of this project is designed to be 70 years;
2.Main equipment:
Sandblasting gun, air pump, recycling device, spray paint gun, spray paint air pump, rubber hose, shovel, hand grinding wheel, sanding cloth, wire brush, cotton thread, small compressor, paint bucket, brush, pickling tank and accessories, etc.
3.Homework conditions:
3.1 Painters should have a special job operation certificate for their construction work.
Before the anti-corrosion coating project, the steel structure engineering has been inspected and accepted, and meets the design requirements.
3.3 The anti-corrosion coating operation site should have safety protection measures, including fire prevention and ventilation measures, to prevent fires and personnel poisoning accidents.
3.4 Outdoor anti-corrosion construction operations should choose appropriate weather conditions, such as strong winds, rain, and severe cold, and should not be carried out.
4.Anti corrosion method:
4.1 The anti-corrosion coating of the project should be carried out after the steel structure installation and acceptance are qualified. Before painting, the rust, weld coating, welding spatter, oil stains, dust and other debris on the parts to be painted should be cleaned up;
4.2 All metal welding joints shall be pre treated with epoxy zinc rich primer to achieve waterproof and anti-corrosion purposes;
4.3 All metal surfaces of the fire water pool and fire pump room, as well as the 200mm wide contact surface between the metal surface and the concrete bottom plate, shall be coated with roller coating or sprayed with silicone fluorine adhesive, with a thickness of 2-3mm. High quality yellow sand soil or yellow sand shall be used for backfilling. During the construction process, it is necessary to avoid damaging the anti-corrosion and waterproof layer. If any damage is found, epoxy zinc rich primer and silicone fluorine adhesive must be used for repair in a timely manner.
Anti corrosion diagram: