Rainwater collection system construction planning
Chapter 1 Construction Organization
1. Construction schedule:
1. Planned start date: as required by Party A
2. Planned completion date: adjusted according to actual conditions
Phase I: Construction preparation (equipment production, transportation, auxiliary equipment procurement, detailed on-site survey, equipment and auxiliary materials entry preparation)
The second stage: support, earth excavation, foundation pouring and maintenance;
third stage: module assembly (assembly of reservoir modules) ;
The fourth stage: equipment installation (water pump, pipeline installation, control cabinet and other major equipment installation) ;
2. Material preparation:
1. Material supply arrangement: From the date of contract signing, materials will be prepared according to the material list and construction drawings in the contract, and the preparation will be completed on July 1 .
2. Material transportation plan: The materials should be transported to the construction site 1-2 days before the third phase ; for the main materials of steel bars and wood panels and some auxiliary materials, they should be purchased on site after entering the site .
3. Outsourced equipment: If necessary, propose and contact the leasing business of large equipment.
4. Record inspection: Unpack and inspect the incoming materials one by one and check the quantity.
3. Construction schedule:
According to the contract period , the system installation and commissioning is planned to be completed within 30 working days after the start of the project (excluding situations where construction cannot be carried out due to bad weather or factors such as Party A’s construction progress). The specific construction schedule is as follows (see next page).
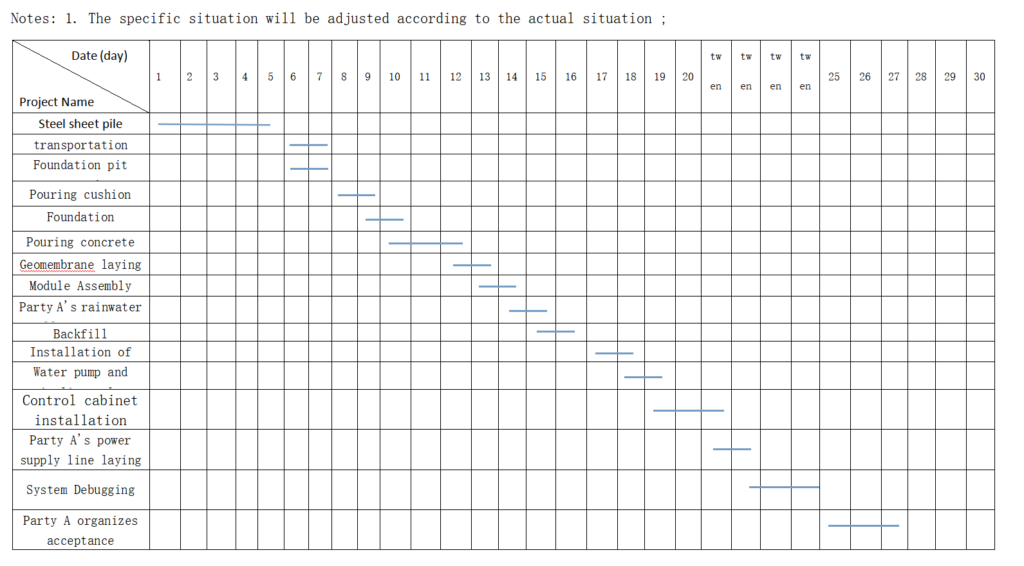
4. Construction organization and technical measures
1. On-site construction manager: Wang Linquan 18261901988 .
2. Staffing: Huang Peng as pile driver, Zhang Yougan as bricklayer and steelworker supervisor , Fei Xiaoqi as water and electricity supervisor, and Zhang Yougan as installation supervisor .
3. Construction basis: contract and detailed drawings.
4. Prepare all the tools.
5. Check the quantity and quality of materials .
6. Check each process
7. Adjust working hours and number of personnel according to the construction schedule.
V. Construction safety assurance measures
1. Safety construction goals
Achieve “Three No’s” and “One Strive”
Three no’s: no major casualties, no major quality accidents, and no major fire accidents.
Strive to: Strive to eliminate work-related casualties
2. Safety management system
a) Safety construction responsibility system
The construction manager is fully responsible
b) Safety construction education system
Level 3 safety education is required for personnel entering the site . Supervision and reminders during construction
c) Safety construction inspection system
Inspect each type of work according to the conditions at the construction site, and point out and adjust any problems found in a timely manner.
d) Safety construction design system
Mainly carry out detailed safety design for weak links in construction to prevent accidents;
Chapter 2 Construction Technology and Methods
1. Project Preparation
After the construction contract is signed, the designer will design the construction drawings, prepare the material preparation list and the project progress chart. Make good preparations for entering the site, familiarize yourself with the user’s site conditions, abide by the user’s rules and regulations, conduct safety operations and civilized construction education before entering the site according to the convention, plan the material list, prepare the materials, and transport them to the construction site. During the material hoisting process, take protective measures to avoid damaging the buildings on the construction site; the materials and tools on site are placed reasonably to ensure that the work is completed, the materials are clean, and the site is clean.
二、Construction conditions
1、13 consecutive working days without rain, subject to the weather forecast.
2、installing the equipment, clean the pool bottom and keep it flat.
3、If there is groundwater in the foundation pit, the contractor will dig drainage ditches around the bottom plate of the pool and a sump at the lowest point in the pool to lead the water that seeps into the pool to the sump at the bottom of the pool. A drainage pump will be installed in the sump to facilitate pumping water at any time during the construction process.
4、During the module installation, the general contractor is required to assist in connecting temporary lighting equipment to ensure the safety of night duty personnel.
三、Foundation pit support, earth excavation and foundation treatment
1、Foundation pit support
In order to facilitate construction and promote the stability of the foundation pit, 4# type 9-meter-long Larsen steel sheet piles are used for support around the foundation pit.
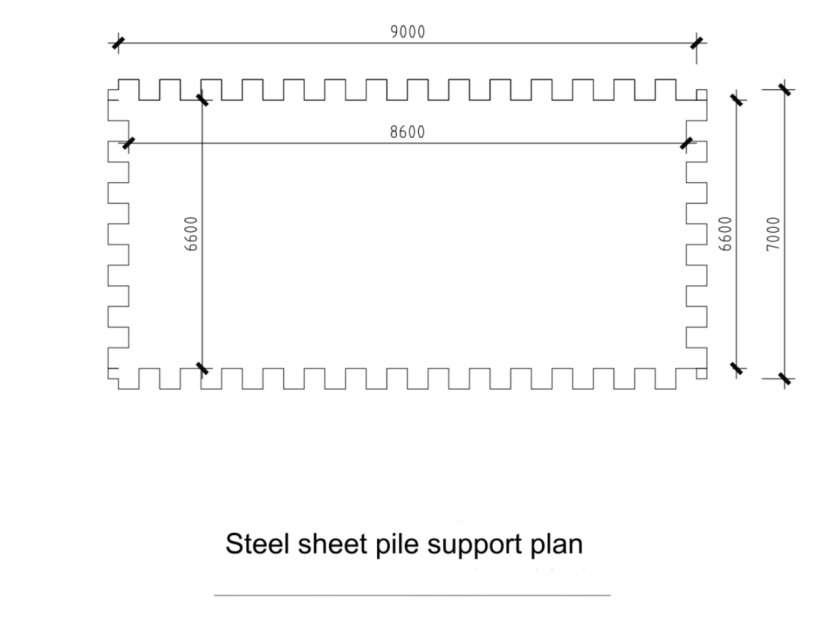
2.Foundation pit excavation sequence
The earthwork excavation is directed by a dedicated person and is carried out by excavator. 20cm is reserved for manual excavation to avoid disturbing the base. Before excavation, temporary drainage facilities should be prepared. The size, shape and depth of each part of the foundation should be constructed in accordance with the design requirements, and the excavation size of the foundation pit should meet the requirements of foundation construction.
3.Foundation pouring
If there is a silt layer under the concrete foundation of the site, make stones to squeeze out the silt layer before pouring the foundation to prevent the foundation from being unstable.
the foundation pit is completed, the longitudinal axis of the base is combined with the cross-section layout to recheck. Only after confirming that the position and elevation are correct can the foundation cushion layer be poured . A C15 cushion layer with a thickness of 100mm is used .
After the surface of the cushion concrete is dry , a line is drawn @250, and steel bars are arranged and tied . A reinforced concrete foundation is adopted, the concrete grade is C 25 , and the reinforced concrete structure reinforcement is single-layer and bidirectional Φ12@250.
4、Excavation depth and width
See construction drawings
4.Installation of geotextile and geomembrane
1.Key points for the installation of geotextile and geomembrane:
1.1 The secondary transportation of geomembrane should be minimized, and the placement location should avoid falling from high altitude or sharp objects on the ground that may damage the geomembrane. The foundation of the foundation pit should be confirmed during installation, and the concrete bottom plate should be cleaned to ensure that the geomembrane is not damaged. After the geomembrane is transported to the site, it is manually rolled and laid. After laying, the geomembrane is inspected to check whether there are any damaged parts. If there are any damages, they need to be repaired.
1.1 Geotextiles and geomembranes should use wide width products, and overlaps and welding seams should be reduced.
1.2 Geomembrane should be welded with double welds to reduce T-seam welding.
1.3 Geotextiles can be overlapped when laid, and the minimum overlap width should not be less than 30cm. A margin should be left for arc-shaped sections. Bricks or tapes can be used to fix them to prevent wind or backfill movement.
1.4 During the geomembrane installation process, operators are strictly prohibited from wearing spiked shoes or other shoes that may damage the geomembrane.
2. This project uses two cloths and one membrane (white membrane: HDPE material)
a.
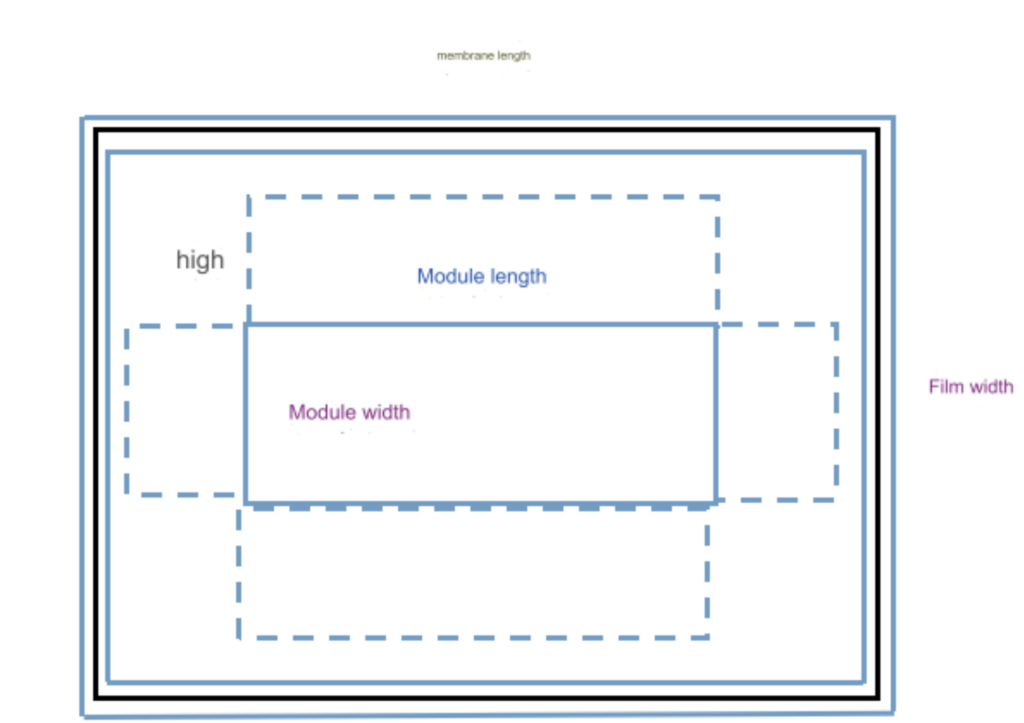
b. The width of the geomembrane is 6 meters. During construction, the membranes need to be welded. The ground is cleaned and the geomembrane is laid flat. A professional welding machine is used. The machine temperature is adjusted to 200~ 300℃ and automatic welding is performed. Geomembrane welding diagram
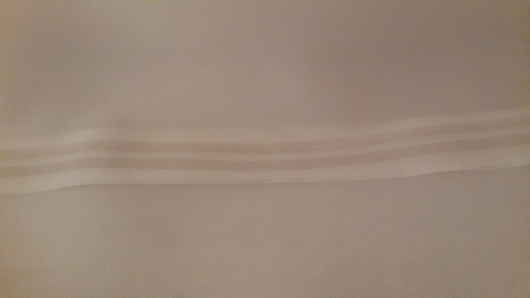
c. Use composite geomembrane to prevent the geomembrane from being scratched during construction.
d. After the module is installed, the top plate geomembrane covers the module to ensure that the top plate is flat.
e. The welding width between geomembranes shall not be less than 100mm.
三、Module Installation
a. Lay out the foundation pit and determine the specific location of the modules. Each layer of modules is completed by splicing the upper and lower parts. A slot is required in the middle of the module. There should be no gaps between the module slots after docking, and the modules should be stacked neatly.
b. The module side panels and modules are connected with slots. Use a plastic hammer to knock to ensure that the module and the side panels are completely spliced. The assembled rainwater module boxes must not be stacked too high to prevent the boxes from falling, cracking or breaking.
c. Use clamps to connect the modules on the same layer and the modules on the upper and lower layers to ensure stable installation between modules. Stacking personnel are not allowed to wear spiked shoes or other shoes that can damage the modules. Stacking personnel are not allowed to push the modules into place on the geotextile and geomembrane.
d. Check the flatness at any time during the paving process. If any unevenness is found, check whether there are foreign objects at the bottom in time. Foreign objects at the bottom will cause damage to the module and the entire system, which may have serious consequences.
四、Module installation completed backfill
The backfilling time should be selected within 48 hours after the water storage module of the pool is assembled and the permeable membrane and cloth wrapped around it are completed, to prevent the groundwater level from being too high, which will cause the module to float up as a whole and cause unnecessary losses. Before backfilling, the water at the bottom of the pool must be pumped out to keep the pool free of water. The backfilling should be carried out around the pool. The backfill soil should be plain soil, and silt should not be used.
1. Backfill the module side
After the module is installed, when there are many impurities in the soil, protective plates should be set around the rainwater storage module pool as a backfill protection layer to prevent the geomembrane from being ruptured due to the squeezing of large-grained stones. The quality of the side backfill is very important to protect the stability of the entire system. Backfill from the side of the module, and prohibit sharp hard objects such as silt and stones from directly contacting the module outer protective plate. Until the soil layer is flush with the surrounding ground plane.
2. Backfill the upper layer of the module
The upper backfill material of the module shall preferably be high-quality soil or original soil , and the thickness of the covering soil shall be backfilled to the designed height or 200mm higher than the on-site soil .
五、 Equipment handling and hoisting preparation work
1. Find out the site and roads for equipment loading and unloading, the installation location and direction of the equipment, and the order of equipment transportation.
2. During the transportation and lifting of equipment, protective measures must be strengthened. When using wire ropes for fixing, the binding of the wire ropes must be firm and reliable, and the center of gravity must be properly selected to prevent eccentricity or slipping, which may cause personal injury and damage to mechanical equipment.
3. When finding the location for lifting the equipment, determine the stress-bearing parts.
4. When hoisting and transporting equipment with sharp angles, protective measures must be taken (such as placing semicircular steel pipes at the sharp angles), and wooden boards, rubber sheets, etc. must be placed between the hoisting rope and the equipment processing surface or corners to prevent accidents caused by the wire rope being cut by the sharp angles.
5. Each wire rope should be evenly stressed, and the angle between it and the vertical line should not be greater than 30.
6. It is strictly forbidden to stand under all hoisting parts, and people are not allowed to stand within the angle of pulling wire ropes. During hoisting, there shall be a dedicated person in charge and everyone shall be responsible for their own duties. If any unsafe factors are found, they must be reported to the commander immediately and dealt with immediately. No one may leave the post without the commander’s order.
7. A trial lift should be carried out before formal lifting. During the trial lift, the lifting equipment should be fully checked. If any problem is found, the workpiece should be put back on the ground first, and the lift should be tried again after the fault is eliminated. The formal lifting can only be carried out after confirming that the trial lift plan is correct.
六、Basic inspection, retest and treatment
The position, geometric dimensions and quality requirements of the equipment foundation shall comply with the design requirements of the construction drawings . The elevation reference line, vertical and horizontal center lines and reserved hole center lines shall be clearly marked on the foundation. Before the equipment is installed, the position and geometric dimensions of the equipment foundation shall be rechecked according to the allowable deviation. The foundation appearance shall not have defects such as cracks, honeycombs, voids, exposed reinforcement, etc.
七、Equipment in place
Hoist the equipment above its corresponding construction site, adjust the equipment position, and align the center line of the equipment base with the installation reference line on the construction site, and then slowly place the equipment on the installation site to avoid vibration and bumps.
八、Water pump and pipe installation
First check the model of the water pump, then tie it into an O-shaped rope, add rubber gaskets, hot-melt weld flanges, check valves, elbows, tees, etc. Pay attention to the heating temperature during welding to prevent cold welding;
九、Pipeline valve installation
1. Valve installation
Before installing the valve, check that the packing gland bolts have sufficient adjustment margin, and valves with flange or threaded connections should be installed in the closed state.
Before installing the valve, check the valve model and specifications according to the design documents, and check whether the valve opens flexibly.
Before installing the valve, the method of tightening the bolts to reduce the spacing must not be used, and the force on each bolt on the flange should be uniform.
2、Pipeline installation
A. On-site inspection of pipes
The inner and outer walls of the pipe should be smooth and clean, without scratches or other defects. No bubbles, cracks, obvious depressions, impurities, uneven colors, decomposition and discoloration lines are allowed. The pipe ends must be cut flat and perpendicular to the axis of the pipe. The working surface of the pipe and the socket must be flat and accurate in size to ensure easy insertion during installation and the sealing performance of the interface. The wall thickness deviation of the same section of the pipe shall not exceed 14%. The curvature of the pipe ≤ 1.0%
B. On-site inspection of pipe fittings
The wall thickness of the pipe fittings shall not be less than the wall thickness of the pipes of the same specifications; the appearance surface must be smooth, without cracks, bubbles, peeling, severe cold spots, obvious impurities, uneven color, decomposition and discoloration and other defects.
D. PPR pipe installation
After the trench excavation is completed and accepted in sections, the PPR pipe can be installed. The pipe cutting should be carried out according to the measured pipe length. The cutting tools should be special pipe shears and cutters, and mechanical cutting should be used for pipes with dn≥40mm. After cutting, the cross section of the pipe should be flat and smooth, without burrs, and the cross section should be perpendicular to the pipe axis.
On the hot-melt butt connection tool, the two corresponding parts to be connected should be aligned so that they are on the same axis and the misalignment should not be greater than 10% of the wall thickness.
Use the milling cutter on the hot-melt butt welding tool to mill the connecting section so that it is perpendicular to the pipeline axis and ensure that the surfaces to be connected are consistent.
Use a clean cotton cloth to wipe off dirt on the surface of the pipe or fitting to be connected, as well as the heating surface of the hot-melt butt connection tool.
Use hot melt butt welding tools to heat the end faces to be connected. The heating time and heating plate temperature (200℃-220℃) should meet the pipe welding requirements. The upper limit temperature should be used for thin pipes, and the lower limit temperature should be used for thick pipes.
After heating is completed, the parts to be connected should be quickly separated from the heater, and uniform external force should be used to make the end faces of the parts to be connected completely contact, and a uniform ∞-shaped flange should be formed at the joint.
The welding pressure, heat absorption pressure, cooling pressure and time of hot-melt butt welding are set according to the instruction manual of hot-melt butt welding.
Butt fusion welding connection ≥110mm, wall thickness>10mm. Socket fusion welding connection<110mm.
After the PPR pipe is connected, the appearance quality of the joints should be checked, and those that do not meet the standards must be reworked.
PPR pipe connections should use the same brand, material and the same pipes and fittings.
E. Installation of PPR pipes and steel valves or accessories
PPR pipes are connected to steel pipes using flange connections, the following requirements must be met:
Another flange (back pressure slip-on flange) should be inserted into the end of the PPR pipe flange connector (follow-type pipe end) to be connected.
According to the PPR pipe connection requirements, the flat end of the flange connector should be hot-melt connected or butt-jointed to the PPR pipe.
The flange gasket should be placed between the steel flange at the metal pipe end and the end face of the flange connector, and the connecting surfaces should fit tightly.
When installing bolts, tighten them evenly in symmetrical positions.
十、Electric control box installation
1、Installation requirements: Use outdoor stainless steel double-door control cabinets and make clear and reliable grounding. The wiring on the distribution box should be arranged neatly and tied in bundles. The wires leading out and in from the panel should have appropriate margins for easy maintenance. The wire stripping should not damage the wire core or make the wire core too long. The wire pressure head should be firm and reliable. Multi-strand wires should not be coiled and crimped, and crimping terminals should be installed. The selection of PE wires should comply with the requirements of Document No. 037. The wires should be color-coded as required, the neutral wire should be light blue, and the PE wire should be yellow-green two-color wire. The distribution box should be installed firmly and flatly, and the allowable deviation of its verticality is 3mm.
2、According to the location and elevation of the control cabinet provided by Party A, the foundation adopts a 100mm thick concrete cushion layer and a brick-built control cabinet foundation. The foundation is buried 200mm deep and 200mm above the ground. It is painted with 1:2 cement mortar, four expansion bolts are embedded, and the grounding electrode is installed. The dimensions of the control cabinet foundation are shown in the figure.
3、Pre-buried PE threading pipe.
4、Marking and positioning: Find the location of the electrical box according to the design requirements, and mark and position it according to the box’s overall dimensions.
十一、Online debugging
1、Preparation before commissioning
1.1 Check whether the direction of the pipeline valve and other installation conditions are correct
1.2 Is the power supply line properly connected?
1.3 Is the reused greening pipeline connected properly?
1.4 Is the water pipe connected properly?
1.5 Is there water in the reservoir? The water level should be at least 1 meter deep.
1.6 Check whether the liquid level signal line, pressure sensor signal line and electric valve control line are connected properly
No-load operation of equipment
2.1 Check whether the voltage of the three-phase four-wire power supply is balanced after power on
2.2 Close the main water outlet valve of the reuse greening pipeline
2.3 Set the thermal relay current according to the motor power of each pump
2.4 Manually start and stop the water pump and check the current and pressure, and adjust the direction of the motor;
2.5 Manually check and debug and switch to automatic operation
2.6 Set the inverter lower limit frequency (25HZ) and upper limit frequency (50HZ)
2.7 Set the liquid level: 0.7 meters for tap water replenishment, stop replenishment at 1.2 meters
2.8 Set the sewage pump to run for 2 minutes
Load operation of equipment.
3.1 First start the recycling pump manually and wait until the official website is fully filled with water (check whether the pressure reaches the set pressure of 0.3MPa) and then switch to automatic operation
3.2 Open the water intake point to check whether the frequency change of the inverter is normal;
3.3 Close the water intake point and wait until the pressure reaches the set pressure of 0.3MPa and lasts for more than 30S to observe whether the inverter enters the dormant state;
3.4 Repeat 3.2 and 3.3 to observe the situation, repeat 3 times, the control system is qualified only after it is correct
3.5 The water pump runs continuously for 2 hours in manual or automatic mode, and check whether there is any abnormality in the motor current.
十二、Completion acceptance
1. The rainwater recycling system has the conditions for linkage no-load trial. We prepare the overall rainwater recycling system linkage no-load commissioning plan and submit it to the owner and the supervisor for approval. We organize the trial according to the approved commissioning plan and notify the owner and the general contractor to participate 48 hours before the commissioning . The notice includes the commissioning content, time, location and the owner. Please make preparations as required and cooperate in the system linkage commissioning. After approval, the representatives of both parties sign the trial record.
2. Completion acceptance procedures
(1) Completion acceptance work procedure diagram
(2) Before the completion of a unit project , the project department shall organize a preliminary acceptance inspection.
(3) After the project department organizes rectification according to the problems found in the pre-acceptance, it will report to the quality inspection department for secondary approval to ensure the smooth completion and acceptance.
(4) After the second-level approval, the project management department sends a completion report to the customer.
(5) After acceptance, the owner, supervisor, quality inspection department, etc. sign and confirm on the handover acceptance statement.
(6) For defects pointed out by the owner during the final acceptance, personnel shall be organized to correct them in a timely manner, subject to the satisfaction of the owner.
(7) Deliver the completion documents to the owner.
Chapter 3 Introduction to Construction Organization and Construction Personnel
1. Organizational Structure:
Our company focuses on rainwater recycling For the equipment supply and installation of the project, the following project construction organizations are specially established:
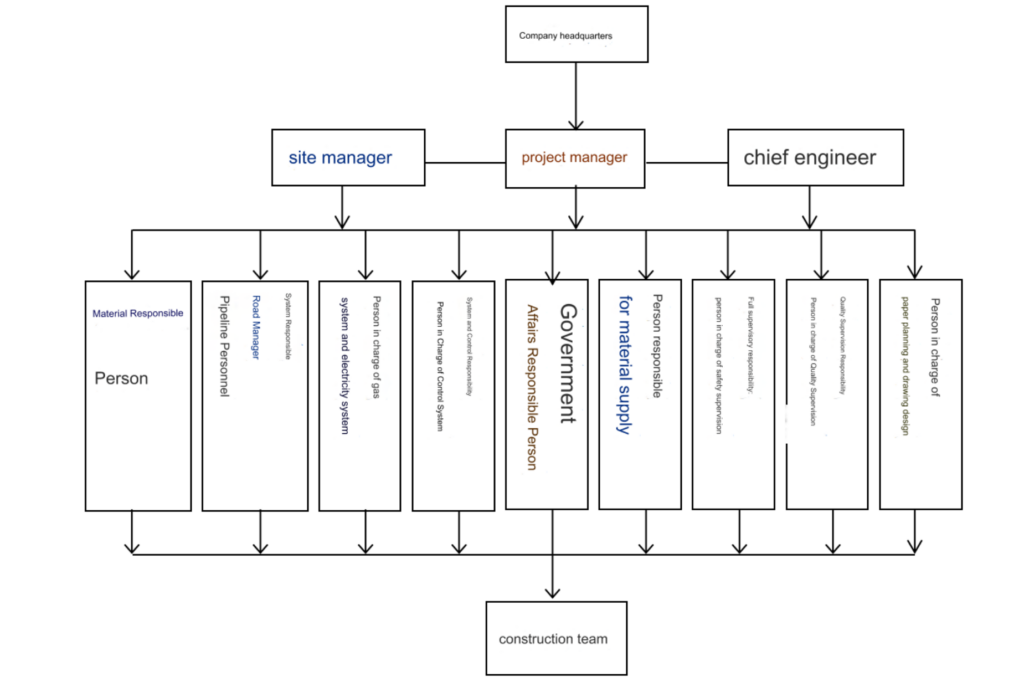
Chapter 4 Safe and Civilized Construction, Environmental Protection System and Measures
1. Safety measures
1. Ensure system operation safety
During the system commissioning and handover, we help the owner to establish the system’s document management, and keep complete completion drawings, design documents, operation and maintenance manuals, equipment lists, etc. for future reference; we ensure the security of the records generated during the use of the system for future reference in case of abnormal accidents.
2. Ensure the safety of construction implementation
Before construction workers enter the construction site, they receive safety education, and at every scheduling meeting, safety is put on the agenda, so that they are always aware of safety and pay attention to it at all times.
Construction site workers must strictly follow the requirements of safe production and civilized construction, actively promote standardized management of the construction site, and organize construction scientifically according to the construction organization design.
Temporary facilities shall be set up according to the general construction plan, and it is strictly prohibited to encroach on the roads and safety protection facilities on site.
All personnel at the construction site must strictly implement the “Safety Technical Regulations for Construction and Installation Projects” and the “Safety Technical Operating Regulations for Construction and Installation Workers”.
Construction workers should use labor protection equipment correctly, wear safety helmets when entering the construction site, and wear safety belts when working at heights. Strictly implement operating procedures and construction site rules and regulations, and prohibit illegal commands and illegal operations.
The installation and use of construction electricity, on-site temporary power lines, and facilities must be carried out in accordance with the “Technical Safety Prevention Measures for Temporary Electricity Use in Construction” (JGJ46-88) issued by the Ministry of Construction. It is strictly prohibited to pull electricity privately or work with electricity.
When using electrical equipment and power tools, they should have reliable protective grounding. Tools carried with you and used should be placed in a convenient and safe place to prevent accidents and injuries.
Protective measures must be taken when working at heights and must comply with the requirements of JGJ80-91 “Technical Specifications for Safety of Working at Heights in Construction”.
The firmness of high stools, ladders, stepladders, overhead cranes, etc. used in construction must be carefully checked before use. Anti-slip measures should be taken at the outer end of the ladder, and it should not be raised for use. When using ladders in passages, there should be someone to supervise or set up fences.
During lifting operations, machinery and slings must first be strictly inspected, and those that do not meet the standards must be prohibited from use to prevent accidents.
In case of force majeure (such as storms, thunderstorms) that affect the safety of certain construction operations, the procedures for stopping operations shall be carried out in accordance with relevant regulations to ensure the safety of personnel, equipment, etc.
The production safety leading group is responsible for inspecting and supervising on-site construction technical safety and keeping records.
2. Civilized construction measures
In order to achieve civilized construction on site and implement the requirements of “strengthening management, fulfilling responsibilities, enforcing laws and regulations, and eliminating violations”, it is required that all construction teams entering the site should follow the requirements of standardized construction sites.
1. After entering the site, you will be responsible for environmental protection around the site, civilized construction, standardized management, and cleaning of the road in front of the door. Before construction, you should carefully survey the construction site, be familiar with the site topography, and flexibly and reasonably arrange the construction work according to the actual working conditions. During the construction process, pay attention to protecting the original facilities, such as pipelines, roof waterproofing layers, lightning arresters, and natural landscapes such as green landscaping and flowers, to ensure civilized construction.
2. Minimize the impact of construction noise and dust on surrounding residents.
3. The construction site shall set up sewage and drainage systems in accordance with the requirements of civilized construction, prepare temporary construction roads and hard sites for material stacking, and keep the site flat and clean.
4. Carry out construction strictly in accordance with specifications, standards and design requirements to ensure construction quality and safety and eliminate barbaric construction.
5. Strengthen the protection of finished products, semi-finished products, products and materials, assign dedicated personnel to take care of them, and establish an entry and exit card system.
6. The layout of water and electricity lines at the construction site must comply with specifications, standards and civilized construction requirements, and must not be dragged, pulled, connected or damaged at will.
7. During construction, drinking water should be delivered to the site by designated personnel, and tea buckets should have safety measures.
8. Strengthen management and strive to create a civilized construction site. All on-site managers must wear badges and certificates to work. All construction operators must wear vests with work numbers to facilitate management. Everyone has the right to stop uncivilized behavior on the construction site.
9. Before construction, construction safety measures must be implemented conscientiously to ensure the personal safety of personnel.
10. During the construction period, the surrounding roads will be kept clean. Pipelines will be properly protected, manholes and sewers will be dredged and kept unobstructed. Straw bags will be laid at the site entrance to prevent vehicle tires from carrying garbage and sludge out of the site.
11. Standardize on-site construction, strictly manage on-site materials and components, and neatly stack them according to the specified classification and specifications. The materials and components are unloaded, transported and stacked in time.
Strict garbage management measures are implemented, and the project department designates special personnel to conduct sanitation inspections, garbage management and removal at the construction site every day. A duty system and a rotation schedule for duty personnel are established to record the day’s sanitation conditions.
Establish a hygiene management responsibility system, a job responsibility system, and a reward and punishment system. The project department will announce the hygiene conditions of the day and implement rewards and punishments depending on the situation.
Strictly abide by relevant government regulations, and do a good job in the standardized construction and transportation of construction debris and building waste during the construction process. Construction debris and building waste must not be dumped or piled up randomly.
III. Environmental Protection Measures
In order to protect and improve the living environment and ecological environment, prevent operational pollution and nuisance caused by construction, and ensure the health of residents and construction workers near construction sites, construction units should strive to do a good job in environmental protection.
1. Organizational measures
Protecting the environment during construction is the owner’s requirement for the contractor, and it is also the contractor’s own responsibility. The construction unit should formulate the “Environmental Protection Implementation Rules” for this project in accordance with the enterprise management standards, national, provincial and municipal regulations, and the owner’s requirements, combined with the specific conditions of the project, and use the specific provisions of the rules as a unified and standardized code of conduct for all construction personnel. At the same time, a special environmental protection staff member is appointed to be fully responsible for the environmental protection work of this project.
Strengthen environmental protection education and incentives, make environmental protection one of the contents of on-the-job training for all construction personnel, and raise environmental awareness. Punish teams and individuals who violate environmental protection.
2. Measures to prevent air pollution
(1) When clearing construction waste, use containers to lift it. It is strictly forbidden to throw it into the air at will to cause dust. Construction waste should be cleared and transported in a timely manner. When clearing and transporting, sprinkle water appropriately to reduce dust.
(2) Fine-grained bulk materials that are prone to flying should be stored in warehouses as much as possible. If stored outdoors, they should be tightly covered. Prevent spillage during transportation and unloading.
(3) It is prohibited to burn toxic or smelly objects in the construction area.
3. Measures to prevent construction noise pollution
(1) Try to control the noise impact during operation, and do not use or use as little equipment as possible that produces excessive noise. Take protective measures during construction to reduce noise to a minimum.
(2) Set up closed operating sheds for high-noise machinery (such as mixers, electric saws, electric planers, grinders, etc.) to reduce the spread of noise.
(3) Promote civilized construction at the construction site, minimize loud noises, do not use loudspeakers or speakers with strange sounds, and enhance the awareness of all construction workers to prevent noise nuisance.
(4) Avoid nighttime construction as much as possible. If necessary, apply for a nighttime construction permit from the environmental protection department in a timely manner and notify surrounding residents. The general contractor shall provide sufficient lighting facilities.
IV. Emergency Plan
During the module installation period, personnel are arranged to be on duty 24 hours a day. The on-duty personnel will go to the site to inspect the situation every 3 hours, including water seepage in the pool, maintenance around the pool, etc., and start the water pump according to the on-site conditions. If there is heavy rain, etc., the inspection efforts need to be strengthened.
1. Heavy rain plan
Pay attention to changes in rainfall during construction. Stop operations when it rains heavily and assign personnel to monitor the site. Park the machinery in a safe area. Carefully carry out rainstorm drainage work at the construction site. The installer will assist and cooperate. According to the site conditions, measures such as ditch modification and water interception will be adopted. Prevent a large amount of rainwater from entering the water storage tank module. Prepare a high-power water pump for temporary pumping work for rainstorms and seepage. Minimize the amount of rainwater entering the water storage module.
2、Collapse
During the construction process, pay attention to the soil conditions around the pool at all times and try to avoid people entering a narrow construction space. If people must enter a narrow space for construction, the general contractor must confirm that the steel sheet piles are firm before entering, and set up a ladder nearby and arrange for people to observe the soil conditions nearby. If there is a risk of landslide, arrange for people to evacuate immediately.
When an accident occurs or a sign of an accident is found, the first person to discover it should immediately notify the person in charge, and according to the situation, he can immediately take the correct method to rescue, report to the relevant personnel or call the police. In the event of a collapse, the personnel should be directed to evacuate quickly to both sides and leave the dangerous area as soon as possible. Quickly judge the development status of the accident and the situation on the scene, take the correct method to rescue, and immediately organize personnel to dig with all their strength after determining the location of the buried personnel; at the same time, cut off the power supply to prevent electric shock. In the process of rescue, it is necessary to prevent secondary earthwork collapse from injuring people, and if necessary, take certain measures for dangerous places first. When the scene does not have the conditions for rescue, immediately ask for help from the society. Analyze the impact range of the earthwork collapse, quickly organize the evacuation of irrelevant personnel from the accident site, and organize security personnel to establish a warning to prevent irrelevant personnel from entering the impact range of the accident. After discovering the signs of an accident, the emergency rescue technical team should quickly formulate effective rescue measures according to the situation and implement rescue as quickly as possible. At the same time, it is necessary to closely monitor the development of buildings, roads, groundwater, etc. around the accident so as to adjust and implement new rescue measures according to the situation.
3、Electric shock plan
During the construction process, the wire interfaces must be sealed with tape and must not be exposed to the outside. If you use power strips, lighting tools, etc., you should pay attention to leakage and bulb explosion when it rains, and cover them with waterproof bags.
When someone is found to be electrocuted, the person should be quickly disconnected from the power source. Generally, the following methods can be used: If the knife switch or plug of the power source is nearby, the plug should be quickly pulled open or unplugged to cut off the power source. However, it should be noted that the general light switch and pull-cord switch are single-wire, which cannot guarantee the disconnection of the phase line (live wire), so pulling open this switch is not safe, and the knife switch should also be pulled open. If the knife switch or plug of the power source is far away from the place of electric shock, the wire should be cut off with well-insulated electrician’s pliers or sharp tools with dry wooden handles (such as knives, axes, shovels, etc.) (after cutting, the live end of the wire should be properly handled to prevent others from being electrocuted). Pay special attention to safety when pulling the wire, and do not pick it if you can pull it, so as to prevent the wire from falling on others. If there is no suitable insulating material available near the scene, and the clothes of the person who was electrocuted are dry, the rescuer can use a dry towel or clothes to wrap his hands to remove the clothes of the person who was electrocuted and disconnect him from the power source. If the rescuer is not wearing shoes or has wet shoes, this method is not used. When the person who is electrocuted is disconnected from the power source, diagnosis should be performed on the spot immediately. However, construction sites are complex and doctors often cannot arrive on site in time. Therefore, it is necessary for every construction worker to have certain first aid knowledge to avoid missing the opportunity.
The person who is electrocuted is conscious but has panic, numbness in the limbs, or has been unconscious for a while but has regained consciousness, he should be made to lie down in a ventilated place and rest quietly. Do not move around. Assign someone to monitor him. No one else should leave and no one should watch. At the same time, call a doctor to measure the blood pressure, respiratory rate, etc. of the person, or carry the person to the hospital for examination and treatment.
4. Mechanical injury plan
When an injury occurs on the construction site, the first person to discover the situation should call out loudly, and the content of the call should be clear: something happened at a certain place or a certain part! The information should be transmitted accurately. Anyone who hears the call has the responsibility to report the information to the project management personnel and rescue team members closest to him, so that the news can be quickly reported to the on-site commander of the emergency response team for casualties and injuries. The project department is responsible for calling the emergency number 120 to report the location and type of injury of the casualties and injuries. At the same time, it must inform the eye-catching landmark buildings near the project to facilitate the emergency center to quickly determine the direction. The project manager is responsible for reporting the casualties and injuries to the company leaders and relevant superior departments in a timely manner. Multiple people should hold the injured person’s body flat and slowly put him on a flat ground. If the injured person has respiratory difficulties, mouth-to-mouth artificial respiration should be performed. If bleeding is found, hemostasis measures should be taken quickly. The proximal end of the wound can be ligated, but it should be loosened every half an hour to avoid necrosis. Arterial bleeding should be stopped by pressing the femoral artery at the root of the thigh.
5、 Module floating plan
Due to the recent rainy weather, sometimes heavy rain in a short period of time, the current top priority is to prevent the rainwater modules installed on site from floating up, and the problem of timely drainage must be solved.
When encountering heavy rain or underground water seepage, resulting in excessive water accumulation on the foundation under the module and around the module, when the module pool rises due to buoyancy, the surrounding soil is soaked by water, the load-bearing capacity is reduced or collapsed. In order to avoid casualties and subsequent safety precautions, the following measures must be implemented:
a. Working principles and scope of application
The principles of unified leadership, hierarchical and departmental responsibility, resource integration, information sharing, division of labor and cooperation, coordination, obedience to the overall situation, emergency disposal, and consistency of power and responsibility. This plan is applicable to the emergency management and disposal of the floating rainwater collection module.
b. When a situation is discovered, a safety alert should be set up in time. To prevent the surrounding soil from collapsing, a safety alert should be set up at a distance from the module, and additional personnel should be assigned to guard the scene, evacuate the crowd, prevent strangers from mistakenly entering the scene, and confirm that no one has fallen.
c. Find out the cause of the floating on site in time. If it is due to the backflow of surrounding rainwater into the module, it is necessary to adopt measures such as ditches and water interception around it. If it is due to heavy rain or underground seepage, it is necessary to use a high-power water pump to temporarily pump out the water. Lead the water outside the site to prevent rainwater from flowing back into the pool.
Specific measures
1、Use a submersible pump to pump water to ensure that there is no water accumulation before covering the soil .
2、After the module construction is completed, the soil must be backfilled as soon as possible to a height of more than 1.5 meters above the module, and reach 200mm above the design elevation or 200mm above the construction site elevation. The width of the soil should be about 1m larger than the foundation pit size to prevent runoff rainwater from entering the soil covering area after rain .
3. Anti-floating measures: soil covering depth ≥ pool height * water density / soil 1.8 * 1.5 safety factor. The soil covering depth of this project should be greater than or equal to 1.5m. After the soil covering is completed, water should be immediately injected into the pool to a depth of 1 meter.
Chapter 5 Construction Schedule
1. Measures to ensure construction period
After the contract is signed, our company will organize the construction plan according to the design plan. The project engineer will organize the construction personnel to conduct technical disclosure after the actual on-site survey in accordance with the construction drawings, and strive to complete the project in advance within the contract period with guaranteed quality and quantity. According to the construction plan, under the condition that the water, electricity and weather conditions of Party A are normal, the project will be completed and delivered to Party A within 30 days of installation.
1. Overall measures to ensure construction period
(1) A project management department will be established on site to work closely with Party A, centrally lead the construction team, coordinate the relationship between various units, be fully responsible for the progress, quality and safety of the project, and ensure the realization of the overall progress from an organizational perspective.
(2) Firmly implement the general spirit of enterprise planning management with completion and production as the goal, take the overall progress in the plan as the basis, take the plan as the leader, implement long-term planning and short-term arrangements, strengthen the dispatching function through the arrangement and implementation of daily plans, maintain the seriousness of the plan, and achieve the goal of completing the project on schedule. Before starting construction, optimize the construction plan of each sub-project to save time and effort while ensuring the quality of each sub-project.
(3) Implement network-based construction, strengthen construction management, focus on the leading processes, arrange sufficient labor, and organize operations.
(4) Make rational use of space and carry out three-dimensional cross-operation.
(5) Promote the flow section construction technology, arrange the work procedures reasonably, manage scientifically, and speed up the progress of the project.
(6) Take practical construction measures to ensure continuous construction and ensure progress and quality.
Regularly and regularly check the implementation of the plan, including the progress of the project, resource supply and management work. During the implementation process, if there is any deviation from the plan, the reasons should be analyzed and scheduling should be carried out decisively to ensure that key processes are carried out as planned.
2. Specific measures to ensure construction period
(1) In the construction deployment, this project can only be constructed according to one flow section, so in order to shorten the construction period, we can only reasonably arrange each process and the cross-operation between processes to reasonably construct. In order to complete this project with high quality and speed, our company will go all out to organize the preliminary construction preparation as soon as possible.
(2) Give full play to the company’s glorious tradition of enduring great hardships, working overtime and continuously, and the advantages of its comprehensive construction capabilities. Seek credibility through quality and seek efficiency through progress. While rationally organizing construction, continuous construction can be arranged in two or three shifts.
The company has listed this project as a key project and will provide strong support in terms of manpower, material resources, funds and technology. It will select management personnel with rich technical experience and strict management to form a project team to ensure that the on-site construction staff are sufficient and have strong technical skills.
2. Technical guarantee measures
1. Sign the construction contract with the owner in a timely manner, complete all commencement procedures promptly, and make a comprehensive and accurate understanding of the actual on-site conditions of the project in advance to ensure timely commencement and smooth construction after commencement.
2. Optimize the construction plan and prepare a reasonable construction process flow chart.
3. Master and apply high-tech, and use science and technology to reasonably speed up the construction progress.
4. Organize bilateral meetings with the construction unit in a timely manner to promptly resolve difficulties and problems encountered during the actual construction process and solve them in a timely manner.
5. Organize the construction team to conduct technical and quality briefings for each sub-project to avoid rework.
6. Adopt follow-up management to solve technical problems in construction as soon as possible.
7. Regularly check the requirements of the construction unit and the construction site, and carry out construction in accordance with the operating procedures.
8. Make full use of the advantages of our company’s construction technology, organize work teams, carry out plane work in different areas simultaneously, and carry out three-dimensional cross-construction to ensure that the construction period goals are achieved.
3. Implementation and adjustment of construction plan
(1) Strengthen the seriousness of the plan, actively organize balanced construction implementation and fully control the plan to ensure the achievement of the construction period goals.
(2) Strengthen the dynamic management of the plan, adjust the plan in a timely manner according to the actual construction situation, and implement an inspection system.
(3) Prepare a general progress plan in advance, identify key processes and key routes, and strengthen control over their actual construction. If a delay occurs, make timely adjustments to ensure that the construction period can be recovered.
(4) Under the premise of ensuring the construction period, in order to reduce the pressure on life and logistics, a labor balance sheet should be prepared to reduce the occurrence of sudden increase in labor.
Prepare daily plans based on the overall construction schedule, compare the actual construction progress with the overall construction schedule, identify and resolve problems in a timely manner, and ensure that the project is completed on schedule or even ahead of schedule.
1. Material supply guarantee measures
(1) Make timely material usage plans for various materials and formulate feasible material supply plans based on actual conditions to ensure that material supply can keep up with construction requirements.
(2) According to the characteristics of the project, timely grasp the market information, adopt a method of multiple channels and fewer links, and direct negotiation between supply and demand parties, sign material supply contracts according to the progress, and specify the date of material arrival.
(3) Strengthen the management of circulating equipment, organize the entry and exit of equipment in a timely manner according to the plan, and ensure that they are stacked neatly and not scattered on site.
2. Measures to ensure the construction period of the installation project
(1) Select an installation project manager who is experienced in installation management and installation technology and has strong management, control and coordination capabilities, and equip him with a management team.
(2) In the early stage of construction, ensure that relevant construction personnel carefully carry out design briefing, provide technical briefing, implement construction technology, and clarify construction procedures in order to solve difficult problems.
(3) Prepare construction equipment plan, labor plan, arrange construction team to enter the site, etc.
3. Construction team guarantee measures
(1) A comprehensive understanding of the technical organization capabilities, construction strength and past performance of each construction team must be obtained, and construction will only be allowed after they are confirmed to be qualified.
(2) The project department and each construction team must sign an agreement to clarify the goals and responsibilities of both parties, and require that a labor balance plan be drawn up based on the contract period, the overall construction schedule, and the phased sub-schedule.
(3) The project department should explain the construction period, technology, quality, safety and operating procedure standards to each construction team.
(4) During the construction process, timely grasp the developments of each construction team, urge each construction team to ensure the number of laborers to ensure the target construction period, and resolutely educate or further punish any construction team that fails to perform its contract.